3d House Design Used In Property Brothers
In a rural area on the outskirts of a town in Southern Mexico, a giant, 33-foot-long 3D printer recently built the walls of the first homes in the world's first 3D-printed neighborhood.
The 500-square-foot houses were finished with roofs, windows, and interiors last week. New Story, the nonprofit leading the project, believes that the new construction process could be part of the solution for affordable housing in some of the poorest communities in the world. "We feel like we've proved what's possible by bringing this machine down to a rural area in Mexico, in a seismic zone, and successfully printing these first few houses," says Brett Hagler, CEO and cofounder of New Story.
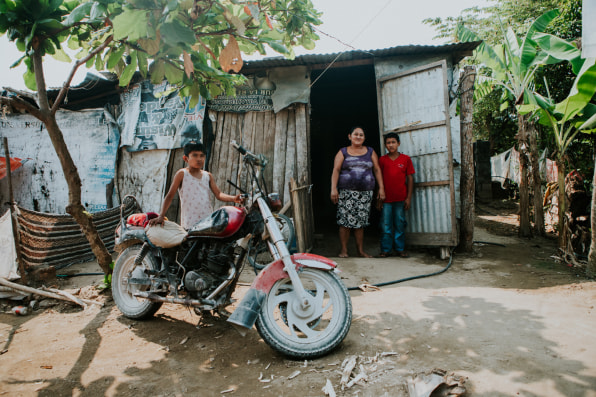
The nonprofit, founded five years ago to bring housing to people living in extreme poverty, has already built more than 2,700 homes in Haiti, El Salvador, Bolivia, and Mexico, using traditional construction. In Haiti, where aid groups struggled to rebuild after the 2010 earthquake, New Story honed a process to work more quickly to finish homes. But it recognized that new technology could help it continue to work faster and decrease costs. Two years ago, it partnered with Icon, a construction tech company based in Austin, to begin developing a 3D printer rugged enough to work even in the most challenging conditions.
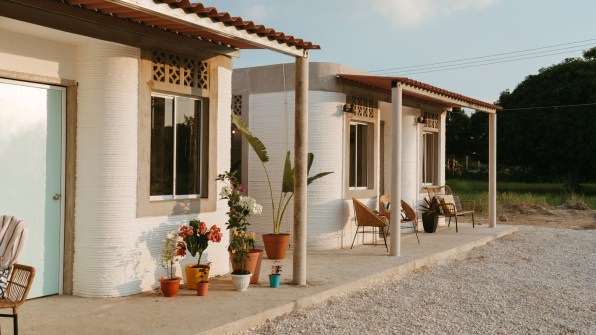
Icon's printer, called the Vulcan II, isn't the first designed to build an entire house. But the new Mexican neighborhood, which will have 50 of the homes, will be the first community to use this type of technology at scale. There have been some other experiments with 3D-printed homes, but they have all occurred in controlled conditions or in areas with little risk of natural disasters, and haven't yet been proven in the real world.
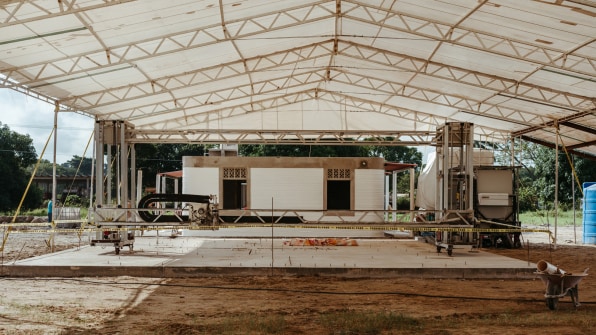
New Story's first-of-its-kind project, unsurprisingly, has faced challenges. The team initially planned to build in another part of Mexico, but because of delays in the process of working with the government to get the land, decided to start farther south in Tabasco, a state that borders Guatemala; the new location faces a higher risk of earthquakes, so the design went through even more structural engineering tests. (The nonprofit hasn't named the specific town to protect the privacy of the people who will live in the neighborhood.)
After the tests were successful, the machine started the long journey south on a truck, but it got stuck at customs for three months. "[The machine] was just a brand new category that obviously didn't exist," says Hagler. By the time the machine made it to the village, the rainy season had started. At one point, the entry to the site flooded, so no one could access it for a week.
But the most important test—whether the printer could print a house on the site—went well. The printer works by squirting a concrete mixture in layers to build floors and walls. Software monitors the weather conditions, and the machine can adjust the mixture. "In the morning it might be drier, and then late in the afternoon, maybe it's more humid, and then you'll adjust that mixture a little bit in accordance to that that you get the viscosity that you need in order to have the same print quality throughout the day," says New Story cofounder Alexandria Lafci.
The team can use an app to make slight adjustments to the blueprint on site, but the printing process is essentially autonomous. To make it even more efficient, it's possible to print multiple houses simultaneously. The first two homes were printed at the same time, in a total of 24 hours over multiple days, because the team wanted to work only in daylight hours; in the future, they hope to run the machine for longer periods, making it even faster. New Story has partnered with a local nonprofit, Echale a Tu Casa, to finish the parts of the homes that can't be 3D-printed, providing jobs to local construction workers.
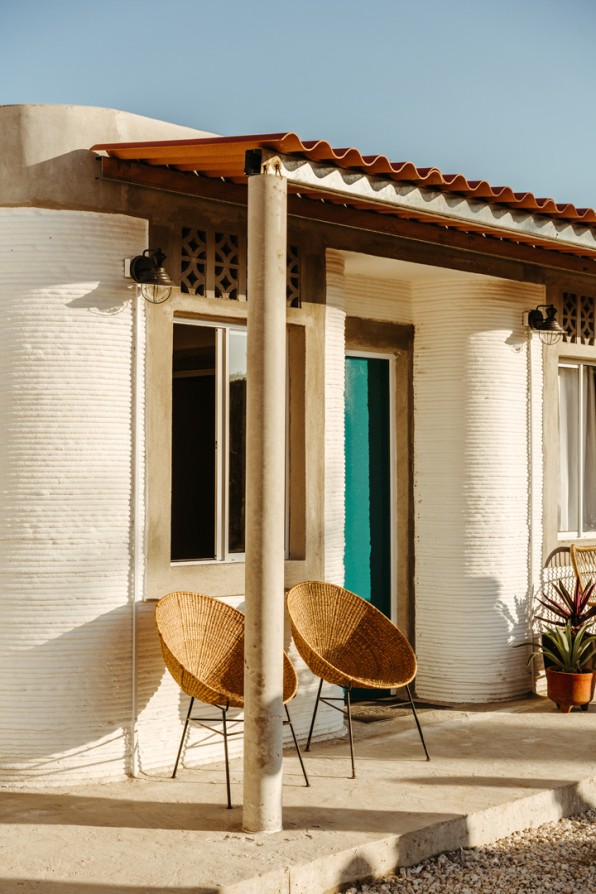
The finished houses have two bedrooms, a living room, a kitchen, and a bath—a vast difference from the simple shacks common in the area. The families who will live in the homes earn a median income of $76.50 a month. "For a majority of the families, this is the first time ever that they will have indoor restrooms and plumbing and sanitation," says Lafci. Unlike shacks, the homes are also seismically sound. The nonprofit partnered with the local government—which is providing both the land and infrastructure like new roads and electricity—to identify the 50 families in the area in the greatest need. Once New Story finishes printing the homes, the new residents own them outright.
Some families toured the first two houses last week, noting how the new homes would stay dry in heavy rain and contrasting it with their current homes. "When it starts to rain, the house starts flooding and it is worse at night," one future resident, Candelaria Hernández, said of the one-room shack where she currently lives with seven family members. "You have to wake up to put pots around the house so it things don't get wet."
The same technology could also help transform the construction of affordable housing in the United States. Earlier this year, Icon printed a welcome center for a master-planned community in Austin, Texas, designed for people who have been chronically homeless, and the company is beginning to print 400-square-foot homes in the community that will be completed in early 2020.
"The homebuilding industry is in need of a paradigm shift," says Alex Le Roux, cofounder and chief technology officer at Icon. "We shouldn't have to choose between things such as resiliency and affordability, or design freedom and sustainability." The company plans to continue to print additional homes and develop the technology. In Latin America, New Story already has interest from multiple other governments that want to donate land to build similar communities, many of which have already visited the new site in Mexico. "Once people see it in person, it's no longer a crazy idea," says Hagler.
The nonprofit plans to continue also exploring other new approaches, acting as a sort of R&D arm for governments that have the resources to build new housing at scale but don't yet have the best tools to do that quickly, and that are looking for ways to do it more affordably. "I think that, like with most of these big, seemingly intractable social issues, there's no silver bullet—you need to have a lot of options of how you're going to solve and target housing," Lafci says. "What we're really passionate about is developing a toolkit of a variety of options of different technologies—be it hardware, software, processes—that we can rely on in order to build homes and build community faster, better, and less expensively."
3d House Design Used In Property Brothers
Source: https://www.fastcompany.com/90440406/the-worlds-first-3d-printed-neighborhood-now-has-its-first-houses
Posted by: dentsuarry88.blogspot.com
0 Response to "3d House Design Used In Property Brothers"
Post a Comment